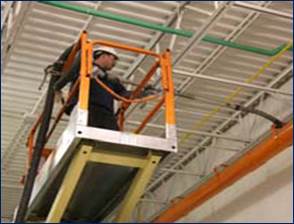
The pace of dust accumulation in a facility can vary greatly. Influential factors include the type and volume of material being processed, as well as the effectiveness of any dust collection equipment installed within the facility.
According to Ashok Dastidar, vice president of dust and flammability testing and consulting services at Fauske & Associates, another key factor is the tendency of the processing operation to “leak” dust into the facility.
“For example, some facilities have mixing or bag dump stations that do not include air sweeps, which are designed to draw away fugitive material,” Dastidar relates. “Additionally, some facilities have sampling ports in the ductwork. These ports are designed to be tightened down. But after years of operation and sometimes improper employee training, the ports are not tightened down every time. You end up with material escaping from the process.”
Depending on the rate of escape, Dastidar says it might take a year for enough dust to accumulate to a level that requires another thorough cleaning. On the other hand, it may take just a few hours. That’s why Dastidar says it’s a smart idea to have a trained professional come in and conduct an audit. “An audit will help determine how the facility should set up its housekeeping protocols,” Dastidar says.
WHERE AND HOW TO MONITOR DUST BUILDUP
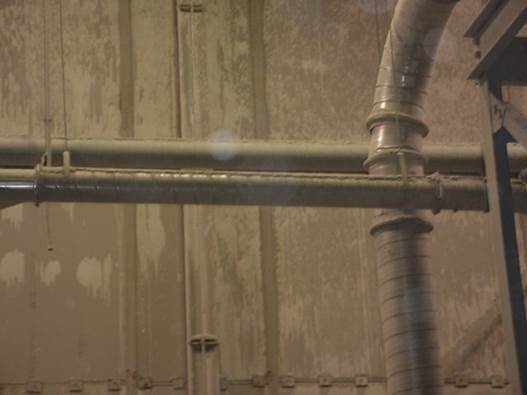
The National Fire Protection Association (NFPA) offers guidance on dust levels. NFPA 654 says immediate cleaning is warranted whenever a dust layer of 1/32-inch thickness accumulates over a surface of at least 5% of the floor area.
“That 1/32-inch standard is based on a standard material density,” Dastidar points out. “If you have a lighter and fluffier material, the standard might be 1/8-inch. Regardless, it isn’t very much. A good rule of thumb is that if you can write your name in the dust, it is too much dust.”
“Another good rule of thumb is dust accumulation that is roughly the thickness of a paper clip,” says Rob Towey, operations manager for Great Lakes Power Vac, a Wisconsin-based provider of industrial cleaning and environmental services since 2004.
To monitor dust accumulation, facilities want to look closely at horizontal surfaces and overhead surfaces. “Simple visual checks are very important,” Dastidar says. “If you see dust accumulating somewhere, note it.”
Dastidar says a good best practice is to set out trays in different locations throughout the facility. Those trays can contain inside markings to help measure the rate of dust accumulation. The trays should be checked weekly at first, and perhaps monthly if the rate of accumulation proves relatively slow. “From there you can back-calculate how long it generally takes for dust to accumulate to the point that it needs cleaning per the recommended standards,” Dastidar says.
It’s important to recognize that the dust coverage area includes the tops of equipment, areas around any dust collection equipment, ducts, and structures such as overhead beams and joists.
“To properly assess dust accumulation in many of those overhead areas, there needs to be close-proximity inspections using a manlift to get elevated to the proper height,” Towey points out.
HOW CAN WE SLOW THE BUILDUP OF DUST?
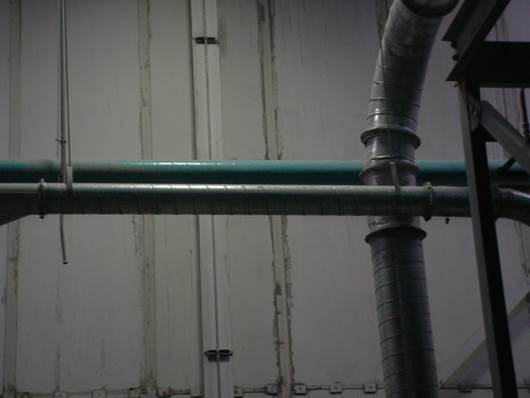
According to Dastidar, the biggest thing a facility can do is “tighten up” its processing equipment to eliminate any dust escape points. All seams and connection points should be inspected for loose fittings and gaps.
The next thing a facility should do is develop a thorough housekeeping regimen. In other words, cleaning up dust can’t be completely avoided. But if cleaning can become part of a more proactive standard operating procedure, facilities can optimize both efficiency and cost.
“Ongoing housekeeping is going to be key,” Dastidar points out. “Sweeping is sort of frowned upon, but not unreasonable. Just make sure you’re using something that is anti-static and contains natural bristle brushes. Also, avoid vigorous sweeping because gentle sweeping will do. When that can’t be accomplished, vacuuming is the best option.”
Industrial cleaning companies like Great Lakes Power Vac can assist facilities in not only the physical work of vacuuming, but also in determining the best equipment for the job at hand.
Frequency of cleaning will depend on the facility and its unique rate of dust accumulation. “Regardless, a facility needs a documented housekeeping program,” Dastidar says. “We tell our clients that their housekeeping program should be just as rigorous as their ISO 9001 QMS program.”
An effective dust cleaning program does not need to be complicated. However, it does need to be documented — and employees need to be trained on it.
“The documentation must be accessible and comprehensible for all custodial staff,” Dastidar says. “Documentation should explain the proper way to inspect for dust, as well as how to sweep, vacuum and wash-down dust.
“Training is the other part,” Dastidar continues. “There must be two levels of training. One is for custodial staff so they know the proper methods for cleaning. The other is general awareness training for all employees. All employees must understand the general concept of dust hazards in the workplace. Employees should also be trained on their important role in the dust management process. Having extra sets of eyes on the problem is a huge help. For instance, an employee on the production line might see material leaking from the system. That employee should understand how important it is to report this to custodial staff so it can be addressed.”
The bottom line is that dust is everyone’s problem — and it should be everyone’s problem to help solve.
ASSESSING DUST HAZARDS IN A FACILITY
The NFPA outlines a 7-step Dust Hazard Analysis (DHA) process for facilities to follow on an ongoing basis.
- Acquire documentation – Thorough documentation helps facility staff gain an understanding of the facility’s inherent risks. Useful documentation includes building plans, piping and instrumentation diagrams, process flow maps, electrical hazard classification drawings, etc.
- Field-verify the documentation – This step is especially important in older facilities where some of the above documentation may be outdated or incomplete.
- Assemble the DHA team – This isn’t a “go through the motions” exercise. Make sure a qualified person is leading an engaged team that includes plant managers, engineers and maintenance personnel, and perhaps even a consultant specializing in combustible dust management.
- Identify hazards and evaluate compliance – Every point in the facility’s operational process must be scrutinized for potential hazards. Those findings must then be documented. Additionally, potential corrective measures should be identified, and existing measures should be re-evaluated.
- Prioritize the hazards – This way the hazards that pose the most risk will be corrected first.
- Document the results – This is important for not only your company’s internal understanding, but also in the event that the facility ever undergoes an inspection. An AHJ (authority having jurisdiction) will likely want to see any documentation you have regarding dust abatement processes.
- Repeat – Combustible dust management is not a “one and done” event. Ongoing attention is required to maintain a safe and compliant facility.